Operational Excellence at LFB
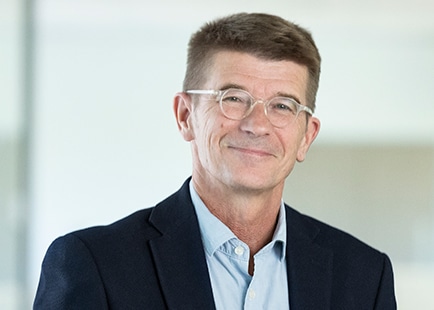
Strategy to achieve Operational Excellence
At LFB, Operational Excellence goes hand in hand with continuous improvement plans implemented across all of LFB's production sites and departments to meet stringent performance objectives.
Several methods have been rolled out to support LFB’s teams:
Lean Manufacturing: this method aims to improve production management while reducing waste, all of which optimises LFB’s performance and productivity and permits it to better meet patient needs. This is a company-wide strategy that concerns every LFB employee.
The Operational Excellence team works specifically with employees to deploy and harmonise Lean Manufacturing tools at LFB’s sites, using the following tools:
This technique uses visual management techniques to monitor and improve the daily performance of teams by activity and by sector, and to hone problem-solving skills.
Management tool that provides an overview of all of the tasks of any given employee at a given time.
This managerial approach consists of “going into the field” to meet with teams and identify problems encountered and possible areas for improvement.
Methodology based on logic and common sense and used to optimise the organisation of the workspace.
This organisational method was developed in Japan and consists of 5 steps:
- Sort, for Seiri,
- Set in order, for Seiton,
- Shine, for Seiso,
- Standardise, for Seiketsu,
- Sustain, for Shitsuke.
A standardised operating procedure that describes the sequence of a tasks to be performed by the technician, with cycle times and photos at each step.
6 SIGMA is a method aimed at improving the quality and efficiency of the company’s production processes. This approach is materialised in several ways. For example, LFB employees at all production sites can be awarded a Yellow Belt, Green Belt and Black Belt upon completing certified training courses taught by the Operational Excellence team, in recognition of their ability to solve more or less complex problems.